Lean, Off The Shop Floor and into the City
Oshawa shows how lean principles can begin to transform local government
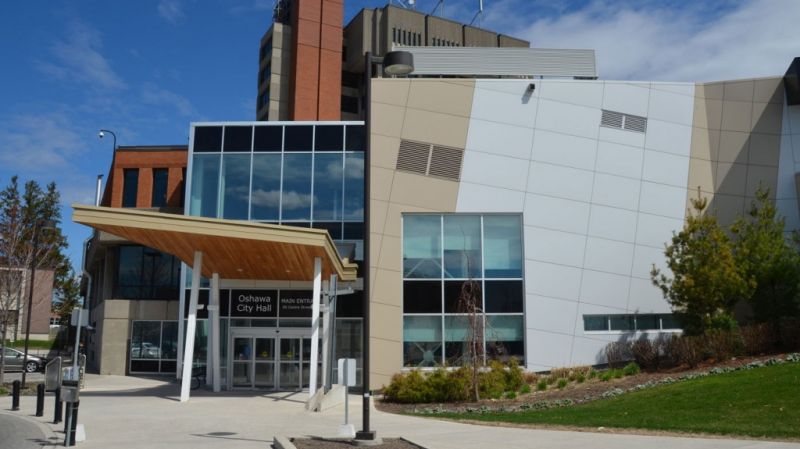
Let’s say someone you know attends a conference and one of the speakers is talking about lean in the services sector. Your friend’s organization is a service operation and, as he listens, the speaker makes very good points about the application of lean principles in a business just like his. He even has a coffee with the speaker after the talk and is further convinced that lean is something he and his team need to pursue.
By the time he returns to work on Monday, he can hardly contain his enthusiasm. Lean will make the business faster, increase both revenue and profit, and, most important, better align his operations to serve the customer. He gathers the leadership team in the conference room and indicates the firm is going to launch a lean initiative, the first of its kind in the business. He talks about what he saw and heard at the conference and why now is the time to make a change: lean will have a huge impact on operations.
As he looks around the room, his excitement wanes. The team seems less than enthusiastic. In fact, by the expressions around the table, it appears his colleagues consumed a bowl of lemons right before walking into the room.
Negative Talk
This is not an uncommon reaction. Think about your own organization and how colleagues are likely to react to the proclamation: We are going lean! Not only are people skeptical, but there are questions and opinions.
- “Isn’t lean a factory or production tool? We are a bank (hospital, municipality, restaurant, hotel, retail operation), not a shop floor.”
- “My wife’s company went through this. They lost 20 percent of their workforce in layoffs.”
- “We tried lean a few years ago, the whole ‘do more with less’ idea. The project died quickly and we went back to the way we had always done things.”
- “I didn’t know we were having financial issues. Isn’t lean something you do to cut costs?”
While hundreds of organizations around the world have successfully applied lean and captured significant value from its principles and processes, there remains numerous misconceptions and a collective misunderstanding of what lean is really about. After several decades of application, many still believe that lean is about doing more with less, headcount or cost reduction, or a focus on shop floor processes. This is largely due to poor execution of initiatives in the name of lean.
In reality, lean is about creating and maximizing value, and applies to all organizations. Without trying to sound Zen, it is a philosophy and way of life for a firm. It is aligned with the reduction of waste and reallocation of resources, in ways that reduce the sort of work that does not create value to support work that does. Lean is strategic, requiring ownership by the top levels of leadership in an organization. The output of effective lean initiatives is an increase in customer enthusiasm, employee engagement, and morale and a reduction in the “stuff” around the firm that drives everyone crazy. Lean builds organizational agility while reducing complexity in its operations. It frees up time to focus on things that matter most.
Lean in the Service Sector
Lean has been applied successfully in plant and manufacturing operations for many years and even in some service sectors more recently.
- Seattle’s Virginia Mason Health Center reduced patient waiting times to virtually zero across all areas of their hospital. The Children’s Hospital of Western Ontario saw similar results in its pediatric orthopedic clinic.
- St. Lawrence Parks Commission freed up resources to support a number of new attractions that are bringing in tens of thousands of new guests every year.
- Airlines and airport authorities are cleaning and turning around aircraft for their next flight in 15 to 20 minutes, less than half the time it took in the past.
- School boards, colleges, and universities are adjusting to changing student and employer needs, demographics, and enrolment patterns, targeting programs to suit the evolving new reality.
One of the more significant opportunities today is government, though with caveats. I have consulted with a number of branches of the federal government as they work to increase their agility and value creation. Untapped opportunities, however, remain at the provincial and, in particular, municipal levels.
We in Canada are all aware of the decrease in transfer payments from federal government to the provincial and municipal level and the corresponding offloading of services to our towns and cities. In many cases, municipalities have responded by amalgamating, consolidating their resources while taking on responsibility for larger populations and geographical areas. While net funding from higher levels of government has decreased, municipalities are expected to keep local tax rates relatively flat and manageable for their local citizens. At the same time, infrastructure demands persist, and investments in quality of life for the population are required every year. A recent study by the Association of Municipalities of Ontario indicates there is an infrastructure gap that would require a property tax increase of more than 8 percent across Ontario to eliminate the deficit. How can a municipality make that work?
A few municipalities in Canada are taking a new approach and shifting their financial and operational paradigms
Large-scale property tax increases are certainly out of the question. Many councils take a “find a way” or “do our best” approach. For these towns and cities, it amounts to making choices — one project versus another — and discussions in council chambers evolve to be long and painful.
A few other municipalities, though, are taking a different approach and shifting their financial and operational paradigms.
The City of Oshawa, Ontario, saw both the challenges and opportunities in front of them. Comments around the council table and administrative offices sounded like this:
- “Infrastructure spending by the new federal government may be available but it’s targeted. Our needs as a city are so broad we can’t rely just on that support. This has to be on us.”
- “The completion of the Durham extension of the Highway 407 Express Toll Route will make it easier for people to commute from Oshawa and for visitors to come here. That will be good for Oshawa but also puts a burden on us in some areas.”
- “We can’t just add bodies. Resources must be targeted to where they add the most value.”
- “We need to stop doing the stuff that doesn’t add value.”
Spearheaded by Jag Sharma, CAO of Oshawa and Queen’s EMBA ’08, Oshawa in late 2015 embarked on a campaign to increase its value creation without increasing spending, and in fact control its own destiny to a far larger scale. Sharma recruited Larry Coté, president of Lean Advisors, to assess the opportunities within city operations. The team established goals of reducing non-value added work while increasing capacity and resources for more important projects around the city.
Promising Results in Oshawa
The initiatives naturally met with some initial skepticism and resistance, especially around the application of lean principles to city operations. Sharma gathered support from forward-minded mayor John Henry, councilor Nancy Diamond (former mayor and chair of the finance committee of Oshawa and a Queen’s alum), among others, and launched several introductory projects. Mayor Henry stated that effective change management that involves front-line employees is the only way to make lasting change. Councilor Diamond pointed out that the city could not keep doing things the same way and expect different results. Oshawa was working to get out in front of its challenges.
Over several months, Sharma, Coté, and the team applied kaizen (continuous improvement), work cell optimization, and other lean tools. The projects targeted Parks and Road Operations, Waste and Facilities, and other areas of Community Services with combined staffing of just under 300 people. Results were not immediate but within just a few months, significant improvements were made.
- Payroll processes were streamlined, cutting associated tasks in half.
- Data entry in Waste and Facility Operations was eliminated.
- Parks and Road Operations cut timesheet entry by 45 percent.
Sharma admits that these gains are small in the overall scheme of things in a city the size of Oshawa, but he realizes the city has to start somewhere. The combination of hard savings and cost avoidance made a significant impact. Their lean journey will be a long one, as is the case with many organizations. As the team gathers experience and enthusiasm, more projects are now underway, including a review of Fleet Operations and further work in Parks and Road Operations.
Credibility for his initiative is increasing among employees, staff, and council members. Through this period, no jobs have been eliminated but responsibilities have shifted. As waste and complexity are reduced, resources can be applied to creating value and a focus on more important work around the city. Staff morale and pride have increased, along with a sense of ownership among employees. Operationally, the city has boosted its ability to get things done, which ultimately is what Oshawans want and are paying taxes for.
Lean has long been applied within the realm of manufacturing and plant operations and more recently within services. Municipalities and other levels of government are now seeing the benefit of a lean philosophy, increasing their agility and ability to create more value. When you think about it, the answer is clear: yes, you too need lean.
Barry Cross is an assistant professor and Distinguished Faculty Fellow in Operations Strategy, and bestselling author of Lean Innovation: Understanding What¹s Next in Today’s Economy.